Introduction to Tilting Table for Precast Concrete
Innovative Design and Efficiency Tilting Table for Precast Concrete
Moldtech’s tilting table for precast concrete are engineered for the efficient production of concrete panels with various thicknesses, ideal for residential, commercial, and industrial structures. The unique tilting mechanism facilitates the vertical removal of panels, significantly reducing the setting time for concrete.
Customization and Advanced Functionality
The tilting functionality is powered by a robust system of telescopic hydraulic cylinders, meticulously calibrated for each table’s dimensions and weight capacity. Operated by a sophisticated hydraulic unit with an electrical control panel, these tables can manage single or multiple tables simultaneously, adapting seamlessly to specific construction project demands.
Benefits of Tilting Table for Precast Concrete
Precast concrete offers exceptional benefits such as strength, durability, and versatility. Manufactured in controlled environments, precast concrete components ensure consistent quality and minimize environmental impact, unlike traditional on-site poured methods.
Overview of Precast Concrete Production
The production process of precast concrete involves several stages: design, manufacturing, curing, and transportation. Each stage is optimized to ensure the final product meets the highest standards of excellence.
Understanding Tilting Table for Precast Concrete
Definition and Purpose
Tilting tables are crucial innovations in the precast concrete industry, designed to mold large, flat concrete panels. These tables allow concrete to be poured and cured horizontally, then tilted to a vertical position for easy removal.
Components and Mechanism
The design includes a robust frame, hydraulic or mechanical tilting mechanism, and a smooth casting surface. These components work together to facilitate the efficient casting and handling of concrete panels.
Advantages of Using Tilting Table for Precast Concrete
Efficiency and Quality Improvements
Tilting tables significantly enhance the efficiency and quality of precast concrete production. They enable faster production cycles, reduce labor requirements, and ensure a high-quality surface finish on concrete panels.
Comparison with Traditional Methods
Traditional casting methods often involve more labor and time, with potential quality variances. Tilting tables streamline the process, reducing errors and enhancing productivity.
Design Features of Tilting Table for Precast Concrete
Material and Structural Considerations
Tilting tables are constructed with high-quality materials and structural design considerations, ensuring durability and the ability to withstand the heavy loads and pressures of concrete casting.
Safety Features and Compliance
Safety is integral to the design, featuring secure locking mechanisms, safety barriers, and compliance with industry safety standards.
The Manufacturing Process of Tilting Tables
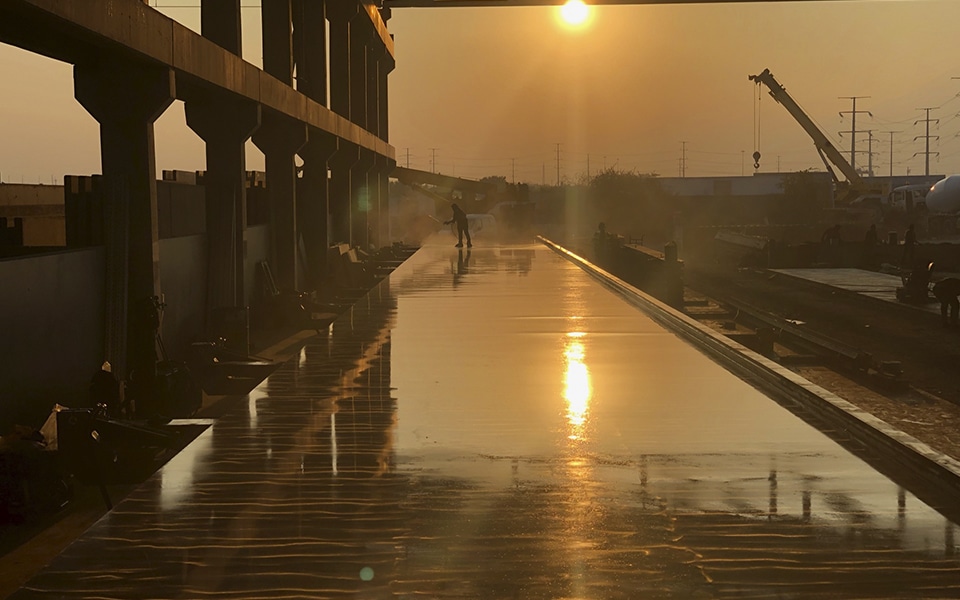
Steps Involved
The process includes preparing the table, pouring the concrete, curing, and tilting the table to remove the cured panel. Each step is crucial for achieving the best results.
Quality Control and Assurance
Quality control is essential in the precast concrete manufacturing process, with regular inspections, testing, and adherence to stringent standards ensuring the finished product’s integrity and quality.
Versatility and Efficiency of Tilting Tables
Moldtech’s tilting tables are designed for versatility and efficiency, with options including fixed, collapsible, or height-adjustable sides. Industrial projects typically prefer a combination of fixed and collapsible sides, while residential projects benefit from more adaptable designs.
Innovative Shuttering Systems
Moldtech integrates flexible shuttering systems, often utilizing magnets. These systems allow for the precise formation of windows and door openings in the panels, ensuring efficiency and versatility in production.
Optimized Panel Production Features
Tilting tables can include an optional vibration system, either electric or pneumatic, to optimize panel production. An advanced finned pipe system with an isolation canvas for heating circulates hot water or steam, significantly speeding up concrete hardening.
Superior Finish and Customer Satisfaction
Moldtech’s tilting tables feature a superior polish on the casting surface, ensuring a mirror-like finish for each panel. This high-quality finish reflects Moldtech’s commitment to excellence, supported by comprehensive operator training for optimal equipment use.
Technological Innovations in Tilting Tables
Automation and Control Systems
Recent advancements include automation and sophisticated control systems, enhancing precision, reducing manual labor, and streamlining the production process.
Future Trends
The future of tilting table technology looks promising, with potential innovations focusing on increased automation, sustainability, and adaptability to various concrete products.
Moldtech’s Case Studies
Real-world Applications
Real-world case studies highlight the effectiveness of tilting tables in diverse scenarios, demonstrating improved efficiency, cost savings, and superior product quality.
Lessons Learned
Analyzing case studies provides valuable insights into best practices, common challenges, and strategies for maximizing the benefits of tilting tables.
Maintenance and Care of Tilting Tables
Routine Maintenance
Regular maintenance, including cleaning, lubrication, and inspections, is crucial for the longevity and optimal performance of tilting tables.
Troubleshooting Common Issues
Understanding common issues and their solutions helps prevent downtime and ensure continuous, efficient operation.
Economic Aspects of Tilting Tables
Cost-Benefit Analysis
A thorough cost-benefit analysis considers initial investment, operational costs, and potential productivity and quality increases.
Return on Investment
The return on investment for tilting tables can be significant, with long-term benefits in efficiency, product quality, and cost savings.
Environmental Impact
Sustainability
Tilting tables contribute to sustainable precast concrete production by reducing waste and improving resource efficiency.
Compliance
They help comply with environmental regulations, reducing the carbon footprint and supporting green building initiatives.
Choosing the Right Tilting Table
Factors to Consider
Selecting the right tilting table involves considering size, capacity, features, and compatibility with existing production processes.
Guide to Selection
A comprehensive guide helps choose the most suitable tilting table model, ensuring it meets specific requirements.
Future of Precast Concrete and Tilting Tables
Predictions and Trends
The future is shaped by ongoing technological advancements, environmental concerns, and evolving industry needs, promising enhanced efficiency and quality.
Potential for Transformation
The continued development of tilting table technology has the potential to transform the precast concrete industry, leading to greater efficiency, quality, and sustainability.
- Precast/Prestressed Concrete Institute – For comprehensive industry standards and guidelines.
- National Precast Concrete Association – For additional resources and industry updates.
- American Concrete Institute – For educational materials and technical documents on concrete technology.
- Engineering News-Record (ENR) – For news and trends in the construction industry.
- Concrete Construction Magazine – For the latest innovations and best practices in concrete construction.
Frequently Asked Questions
How do tilting tables improve the quality of precast concrete?
Tilting tables ensure uniform thickness and consistency, leading to higher quality finishes. The horizontal casting surface reduces defects and provides a superior surface finish.
What safety features are essential in tilting tables?
Essential features include sturdy construction, secure locking mechanisms, safety barriers, emergency stop controls, and tilt angle limits. Regular maintenance and inspections ensure safety features function correctly.
Can tilting tables be customized?
Yes, tilting tables can be customized to suit specific precast concrete products, including size, shape, surface texture, and reinforcement needs.
How do tilting tables impact the cost of precast concrete production?
Tilting tables reduce overall costs by increasing efficiency and reducing labor. While the initial investment is significant, long-term savings and improved product quality offer a favorable return on investment.
What are the environmental benefits?
Tilting tables reduce waste and improve resource efficiency, supporting sustainable practices and green building initiatives.
How does automation enhance the process?
Automation increases precision, reduces manual labor, and streamlines production, resulting in higher efficiency and consistent quality.
Related content
- Equipment for Precast by Moldtech
- Precast Concrete Moulds: Leading the Revolution with Moldtech
- Moulds for Precast Concrete Products: Icon of Modern Construction
- Precast Concrete Plants: Construction Efficiency with Moldtech’s Advanced Solutions
- Precast Concrete Mouldings: Revolutionizing Modern Construction
- Precast Concrete Factory: Best Equipment Manufacturer